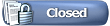 |

03-06-2005, 11:37 AM
|
 |
Administrator
|
|
Join Date: Dec 2004
Location: Valley Forge, PA
Posts: 1,598
|
|
Heat treating AK receivers...
NOTE: I have updated these directions into a new thread....
Please See:
http://www.quarterbore.net/forums/showthread.php?t=541
I am closing this thread so that all new posts go to the new thread!
|

03-06-2005, 11:43 AM
|
 |
Administrator
|
|
Join Date: Dec 2004
Location: Valley Forge, PA
Posts: 1,598
|
|
So far I have done three builds... My first were using OOW receivers that were already heat treated. The last is a Tapco Flat that we needed to heat treat...
We heat threated my flat using the following basic steps...
1. heat all areas of receiver that has holes for pins or rivets as well as the ejector rail tip with a MAPP torch until bright red.
2. Quench the Receiver in motor oil
(Note do above one or two holes at a time)
3. Reheat receiver parts as described above to a dull red.
4. Allow receiver to cool at room temperature.
Note: When using the MAPP torch I was warned to use a broad flame when heating as opposed to one of the cutting type heads! Also, this was an AK pistol that I really don't shoot much so while I have not had problems it needs to be said that I may only have 100-200 rounds through the gun!
|

03-06-2005, 11:49 AM
|
 |
Administrator
|
|
Join Date: Dec 2004
Location: Valley Forge, PA
Posts: 1,598
|
|
Now, I was looking at AK-47.net and found this method...
http://www.gunsnet.net/forums/showthread.php?t=229481
Posted 02-15-2005, 02:06 PM
By High Road
Quote:
Ok here goes at what I do. I have a steel pan for sheetrock mud that i use to hold the Kasenit in. I clamp my receiver with a pair of channel locks and put that in a vise. I then heat up the entire receiver with Mapp gas tourch until red hot. Then with a leather glove on, I grab the channel locks and put the receiver in the pan of Kasenit and cover it from head to toe. I then remove and quench in either oil or just cold water. Heat it all up again to a dull red and let cool down on its own. Works for me. And you can deffintely tell that the receiver shell is harder, more durable. Kasenit does surface hardening, which is plenty for an ak receiver. Brownells Catalog #57 page 170 item # 479-001-100 Used to obtain a super hard surface on low carbon steel. $9.00 for a 1lb. can.
|
Also, POKIE has info on how he did his on his website:
http://pookieweb.dyndns.org:61129/AK.../heattreat.htm
http://pookieweb.dyndns.org:61129/AK...tion/rails.htm
I welcome any updates or other suggestions...
|

03-06-2005, 11:54 AM
|
 |
Administrator
|
|
Join Date: Dec 2004
Location: Valley Forge, PA
Posts: 1,598
|
|
EDIT & NOTE: This post was in relation to Pokie's site and he had admitted that he had an error there and it may be changed by the time you read this... The methods described above and in the new post are the correct way to heat treat an AK receiver...
Look at POKIE's site ( http://pookieweb.dyndns.org:61129/AK.../heattreat.htm)
He clearly indicates that we want to slowely cool after the fist heat and quickly cool after the second step. I am sure this is opposite of what I had done and opposite of most advise I have seen... Is Pokie's advise wrong or am I wrong? Anybody!?!? :shock:
|

03-06-2005, 12:00 PM
|
 |
Administrator
|
|
Join Date: Dec 2004
Location: Valley Forge, PA
Posts: 1,598
|
|
Here is another VERY detailed discussion:
From http://www.gunsnet.net/forums/showthread.php?t=155829
Quote:
Spray & Pray posted a method awhile back that I've used quite successfully. Here it is:
General ghetto tech heat treat for medium carbon steels (4130). This is how I do it, but no recommendations or warrantees are expressed or implied here. This is for entertainment purposes only, the post below involves high temeratures, flammable and/or explosive gasses. Proceed entirely at your own risk. You could very easily hurt yourself & others and/or damage property and/or end up with a FUBAR'd receiver. I am well know having a loose grip on reality and to play fast and loose with the truth, blame anyone but me for any misfortune that befalls you. If things work out for you though, a small gratuity would be nice
Step 1: Heat the desired area to temerature it becomes non-magnetic.
On 4130 this equates to dull orange color, approximately 1550° F. The easiest way to find the correct temperature is to heat a scrap of the material with a torch and test the attraction of a large magnet as you heat it. It will be obvious when the steel looses its attraction for a magnet. Note the color of the steel at this temperature. Color of steel is a very good indicator of temperature. With a little practice you can recognize the correct color and it will always be the same color for that particular alloy. It would be nice to post a picture of the correct color, but with uncorrected color on my cheap camera, and unknown correction on different monitors displaying the picture, it could cause errors. A big/strong magnet and a test run on scrap will leave no doubt about the correct color.
Step 2: As soon as you have heated the area to be hardened to the correct color, quickly quench it.
Medium carbon steels like 4130 do best with a water quench. Higher carbon steel alloys will overharden in a water quench and break or shatter from internal stresses, they require an oil quench. There are some high tech alloys that require an air-quench and will shatter when quenched in oil. Low carbon steel won't harden well with any type of heat treatment and require case hardening. If you don't know what alloy you are working with, you will have to test a scrap and see what gives a satisfactory quench. Heat a scrap to non-magnetic color and quench it in oil. Test with a file to see if it is hardened. A file should have a very difficult time marking a hardened, undrawn piece. If it isn't hardened, heat it back up and quench in water. See if it shatters when quenched, if so it is a oil quench alloy. Test the hardness with a file. If it hasn't hardened much with a water quench, you have a sample of low carbon steel which can be case hardened, but won't heat treat.
Quenching water should be luke warm. Transmission fluid makes very good quenching oil. When quenching in oil, be prepared for smoke and the possibility of the oil igniting.
Step 3: After quenching, the material will be very brittle and requires drawing some of the hardness. Heat the piece to the correct temperature to draw and let it air cool.
The correct temperature to draw 4130 is about 700° F. The easiest indicator for this temperature is the metal should turn a blue color under good lighting, almost looking like blued gunmetal. Once it reaches the temperature and turns blue the color will persist after cooling. The blue color can be rubbed off with a wire brush or sand paper. The way I reach this temperature is to pre-heat the whole receiver (with spot hardened points already done) in my kitchen oven. My oven only goes to 550° so I preheat the receiver to that temp for 45 minutes. When preheated, I open the oven door just enough to get a propane torch flame on the spot hardened points. I quickly heat them to the "blue" temperature, it requires good light on the receiver to see the color change well. As soon as all points are "blued" (about 15-20 secs per point direct flame), I shut the oven door and let the temperature inside stabilize. I then shut off the oven and allow to cool normally without opening the door till cool.
Various notes and observations:
Testing scraps of metal will demonstrate heat treating better than any written instuctions. A three corner file is a great "ghetto tech" testing tool that will show what happens at each step. File on an untreated scrap with the corner of the file. It will cut a notch easily. Harden the same piece by heating and quenching. Now the file has a tough time even marking the steel. Bend the hardened scrap, hit the scrap on an anvil. Cracks and breaks, doesn't it? Draw the temper in an oven. Now the file will cut, but not as easily as on an untreated scrap. Hit it with the hammer, it shouldn't break, but it should be less ductile than an untreated scrap.
There is a broad range of hardness that you can draw to by changing the drawing temperature and time, and the cooling rate. This is mostly beyond the scope of at home "ghetto tech" but it is fun to experiment. Less temperature and time spent on drawing will yield a harder and more brittle treatment.
When a receiver is spot hardened, as opposed to heat treated in its entirety, a "composite" structure is created. This composite structure can be made superior to any whole-unit heat treatment. The structure of the receiver can be made superhard at the points that require hardness, yet the hard points can be supported by unhardened areas adjacent to the hardened spots. This support allows a harder area to keep from cracking or breaking than is possible in a receiver that is heat treated all over. A receiver that is treated whole will "ring like a bell" which shows that vibrations are travelling through the receiver where they can concentrate stresses at specific areas and crack them over time. A spot hardened receiver will have a "duller" sound when struck, which shows that vibrations are damped out and absorbed throughout the receiver. In no way would I claim that a home "ghetto teched" spot hardened receiver is superior to one done at a professional heat treating shop. With a little practice it is easy to treat one at home where the heat treament won't be an issue though. It is pretty easy to do it "good enough" for a long lasting AK.
|
|

04-20-2005, 01:31 AM
|
 |
Administrator
|
|
Join Date: Dec 2004
Location: Valley Forge, PA
Posts: 1,598
|
|
A few more captured oppinions from AR15.com
http://ar15.com/forums/topic.html?b=4&f=51&t=70601
Quote:
TheNorm
Joined :: May 2004
Post Number :: 175
TX, USA
Just did one and learned a little more...
I didn't heat treat the ejector before installation...which is a mistake since it's easier with it out of the gun.
The first time I heated to cherry red, then quenched in oil. I took it out and after about 60 rounds, the ejector tip started to deform a little. I figure it would have failed completely (by bulging and causing the bolt to jam) in about 300 rounds.
So I re-shaped it and heated to cherry red, HOLDING for 3 minutes at that temp. Then I quenched in oil (poured half a quart of fresh oil over it over about 30 seconds). Then I heated to get the blue color and held that for about 30 seconds.
Shot about 300 rounds through it and there is no sign of deformation, so it looks like it worked. Note that I am using steel case ammo, as most of us are with 7.62...
So there's my 2 cents...
|
and
Quote:
kidcaos
Joined :: September 2004
Post Number :: 185
You should look into the product Kasenit. You heat the part until cherry red, then immerse it into this stuff, then reheat to cherry red and quench in cold clean water. Really simple.
|
|
Thread Tools |
|
Display Modes |
Linear Mode
|
Posting Rules
|
You may not post new threads
You may not post replies
You may not post attachments
You may not edit your posts
HTML code is Off
|
|
|
All times are GMT -4. The time now is 02:38 AM.
|