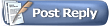 |
|

02-18-2010, 07:38 PM
|
Junior Member
|
|
Join Date: Feb 2010
Posts: 23
|
|
Scalce
Thanks for the reply. I have about 20k of .223 brass so I figured I would turn a couple 2-3 thousand into Whisper. I need to process the .223 brass anyway, so I was already planning on getting a RT-1200 for that. Adding the C-H trim die is affordable in comparison, so I figured what the heck.
Thanks again
jonblack
|

02-19-2010, 10:35 AM
|
Senior Member
|
|
Join Date: Dec 2009
Location: Greenville, SC
Posts: 125
|
|
Quote:
Originally Posted by jonblack
Scalce
Thanks for the reply. I have about 20k of .223 brass so I figured I would turn a couple 2-3 thousand into Whisper. I need to process the .223 brass anyway, so I was already planning on getting a RT-1200 for that. Adding the C-H trim die is affordable in comparison, so I figured what the heck.
Thanks again
jonblack
|
Ahhhhh
A brass whore after my own heart.
Are you going to just use one specific headstamp?
If you do go with the 1200 then you just need the FL sizer and seater dies along with the C&H trim die.
|

02-20-2010, 12:52 AM
|
Junior Member
|
|
Join Date: Aug 2009
Posts: 18
|
|
I made 200 pieces using virgin LC brass today and it was a piece of cake!
I like the fact that the necks came out much more concentric than the 221 Fireball brass I used before.
|

02-21-2010, 01:42 AM
|
Senior Member
|
|
Join Date: Jan 2010
Posts: 118
|
|
300/221 brass
Thanks for the suggestions! I have a Harbor Freight fairly close to my home and after reading thru the article had to give this method a try.
Unfortunately, the first saw only turned on about a half dozen times, then the switch went out. The second one is still working. The very first thing that should be done after unpacking it is to remove the blade cover and reinstall the screw that holds the blade in place with Loc-tite or similar compound! The blade on my assembly almost came completely undone while cutting brass.
I used the suggested method with an old .308 case but was having a hard time getting even cuts so I tried this...
Take a 1 1/2" x 1/2" piece of wood and cut two lengths between 4" and 6":
Place them together and drill a 1/4" pilot hole:
Using the pilot hole drill out to 3/8":
Now that your working with a 3/8" hole, use a 3/8" spade bit and drill to the depth of the original .223 shoulder:
Set the new wood channel in-line with the .308 case, once aligned tighten the clamp:
With this setup I was able to get a good, clean, straight cut on the brass and minimize the work needed on the much more exact trimmer blades:
|

02-21-2010, 04:20 PM
|
Junior Member
|
|
Join Date: Feb 2010
Posts: 23
|
|
Scale
As for the brass I use to make .300 Whisper, yes, I will sort it by head stamp. I will most likely sort my LC stuff by year as well, just to provide another level of uniformity.
As for the .223 I process, I won't sort by head stamp.
jonblack
|

04-30-2010, 05:25 PM
|
Senior Member
|
|
Join Date: Dec 2009
Location: Greenville, SC
Posts: 125
|
|
Quote:
Originally Posted by N310toN170
Thanks for the suggestions! I have a Harbor Freight fairly close to my home and after reading thru the article had to give this method a try.
Unfortunately, the first saw only turned on about a half dozen times, then the switch went out. The second one is still working. The very first thing that should be done after unpacking it is to remove the blade cover and reinstall the screw that holds the blade in place with Loc-tite or similar compound! The blade on my assembly almost came completely undone while cutting brass.
I used the suggested method with an old .308 case but was having a hard time getting even cuts so I tried this...
Take a 1 1/2" x 1/2" piece of wood and cut two lengths between 4" and 6":
Place them together and drill a 1/4" pilot hole:
Using the pilot hole drill out to 3/8":
Now that your working with a 3/8" hole, use a 3/8" spade bit and drill to the depth of the original .223 shoulder:
Set the new wood channel in-line with the .308 case, once aligned tighten the clamp:
With this setup I was able to get a good, clean, straight cut on the brass and minimize the work needed on the much more exact trimmer blades:
|
Nice work with the wood holder.
Freehanding sucks because you can cut it at an angle, cut it and leave a nice tab of sharp metal to shave off, etc..
It completes our inexpensive method of trimming 300 Whisper brass.
BTW My chop blade also loosened so I had to tighten it.
|

08-29-2010, 09:44 PM
|
Junior Member
|
|
Join Date: Aug 2010
Location: South Florida
Posts: 8
|
|
Hello,
Has anybody considered the 6" chop saw that HF sells for trimming the brass? It costs another $5 but could be usefull for other projects.
http://www.harborfreight.com/6-inch-...saw-41453.html
I am a newbie here, so any help or advice is happily accepted.
Thanks,
Regards,
Fred
|

09-16-2010, 12:11 PM
|
Junior Member
|
|
Join Date: Aug 2010
Location: South Florida
Posts: 8
|
|
Scalce and N310toN170,
Thanks for posting this system of trimming the .223 brass for 300 whisper conversion. I am using it and it works great. Before I started cutting any brass I used locktite on everything that I read about in your threads, and the little saw is working great.
Regards,
Fred
Last edited by pelallito; 09-16-2010 at 12:28 PM.
Reason: spelling error
|

09-16-2010, 11:17 PM
|
Super Moderator
|
|
Join Date: Mar 2010
Posts: 281
|
|
I know it is a little different than what is posted here, but I have picked up a Redding file trim die for the 300w, what is the proper method for using these?
|

09-17-2010, 08:51 AM
|
Junior Member
|
|
Join Date: Aug 2010
Location: South Florida
Posts: 8
|
|
Maybe this will help-http://www.midwayusa.com/viewProduct/?productNumber=757107
In the comments someone stated that they use a fine hacksaw blade to cut off the top of the case. Someone else said he needed an extended shell holder to make it work.
Fred
|
Thread Tools |
|
Display Modes |
Linear Mode
|
Posting Rules
|
You may not post new threads
You may not post replies
You may not post attachments
You may not edit your posts
HTML code is Off
|
|
|
All times are GMT -4. The time now is 09:33 AM.
|