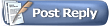 |
|

01-27-2010, 11:12 AM
|
Junior Member
|
|
Join Date: Nov 2009
Posts: 25
|
|
I tried using the Wilson case holders but they wouldn't fit in the jaws of the HF mini cut off saw's vice so I tried your .308 case method. Had to open up a fired case just a touch more to get the resized .223 case neck in but it works pretty slick. Your brass jig is a definite enhancement over anything I was dreaming up. Thank you for sharing the tip!
One thing I've noticed on the HF saw is that it's a bit underpowered and leaves a fairly ragged cut (OK it's cheap). I wonder if I'm just trying to cut too fast and since I don't have it anchored down perhaps I'm inducing more flex than it would otherwise have, so I'll try it again with better anchoring. I do wish the blade was a bit finer toothed, but it's the best tool I have for this purpose and it's a heck of a lot better than the hacksaw or tubing cutter method I tried previously.
I'm doing the final trimming on the Giraud and it's doing its typically great job once I got the blade adjustment set.
Thank you again.
|

01-27-2010, 11:12 PM
|
Senior Member
|
|
Join Date: Dec 2009
Location: Greenville, SC
Posts: 125
|
|
Yeah I agree on the lack of power and that a finer tooth blade would cut much cleaner.
If you go too fast the blade will slow which is probably what is happening to you.
You can always put an old file next to the mini saw and drag the brass across it to get the nasty burs off but I haven't had too much of an issue trimming while it has a rough edge.
Hopefully my barrel comes in soon so I can start producing properly sized cases.
Happy trimming
|

01-28-2010, 12:54 AM
|
Junior Member
|
|
Join Date: Nov 2009
Posts: 25
|
|
Well, I just came in from the garage where it became obvious why my blade on the Harbor Freight saw was dragging and stopping when I smelled hot plastic after making 2 and a half cuts on cases.
I pulled the guard off the left side and had quite an accumulation of rubber debris from the belt where it was slipping because the saw driving cog was't adequately secured and was slipping on the shaft. That resulted in extra heat buildup and the cog rested against the belt cover melting an indentation in it. Oh joy! I tried securing the set screw on the saw driving cog but it acted like it was stripped and I didn't have any metric replacements on hand
I must have received one made before some Chinese national holiday. When I originally pulled it out off the box I noticed the cord cover was outside the housing too but I didn't worry about that as I wasn't planning on stressing the cord. Reminds me of a Volve Turbo I once owned that must have been made the afternoon before Swedish summer holiday. What a piece of crap that was.
Now to see what Harbor Freight is willing to do about it. Guess I got what I paid for and less....
Update: I called HF customer service and they're sending a prepaid return Fedex label for return credit since I'm within 30 days of purchase. I have a local HF store I wasn't aware of and I'll pick up a replacement there as they won't take a mail order return. Suboptimal, but not bad in all.
The saw may not be as underpowered as I thought given the slipping drive belt I was experiencing. It will never be a powerhouse but seems to be adequate for the task and saves a lot of brass shavings.
Last edited by PFDD; 01-28-2010 at 11:30 AM.
Reason: New info
|

01-29-2010, 04:21 AM
|
Junior Member
|
|
Join Date: Mar 2005
Location: SE-ID
Posts: 26
|
|
Great pictures, love your jig, I think it will work better than mine.
I bought some little abrasive fiber wheels to use on the saw they seem to work just fine.
Now to get that power trimmer...
|

01-30-2010, 11:30 AM
|
Senior Member
|
|
Join Date: Dec 2009
Location: Greenville, SC
Posts: 125
|
|
Quote:
Originally Posted by sten668
Great pictures, love your jig, I think it will work better than mine.
I bought some little abrasive fiber wheels to use on the saw they seem to work just fine.
Now to get that power trimmer...
|
Glad I could help.
What size blades does your cutter take?
Also what trimmers are you looking at?
|

02-06-2010, 10:46 PM
|
Junior Member
|
|
Join Date: Mar 2005
Location: SE-ID
Posts: 26
|
|
I have the same cut off saw. So I got blades that fit it, can't say of the top of my head, they may be just a little larger. The trimmer that you have is what I have been looking at but my drill press is out in the shed with no heat and the forester hand trimmer has been working....slow.
The problem I am having now is that the mill brass I have is not sizing down enough to fit in my new M1S barrel unless I use another 223 die to get it smaller. My have to go with a small base die for 100% reliability in my auto and keep the brass separate from my bolt gun stuff.
|

02-07-2010, 01:24 PM
|
Senior Member
|
|
Join Date: Dec 2009
Location: Greenville, SC
Posts: 125
|
|
Quote:
Originally Posted by sten668
I have the same cut off saw. So I got blades that fit it, can't say of the top of my head, they may be just a little larger. The trimmer that you have is what I have been looking at but my drill press is out in the shed with no heat and the forester hand trimmer has been working....slow.
The problem I am having now is that the mill brass I have is not sizing down enough to fit in my new M1S barrel unless I use another 223 die to get it smaller. My have to go with a small base die for 100% reliability in my auto and keep the brass separate from my bolt gun stuff.
|
So even with the press camming over, the 300 die is not resizing enough for you?
Have you tried resizing the cases in your 223 dies before forming?
|

02-07-2010, 06:22 PM
|
Junior Member
|
|
Join Date: Mar 2005
Location: SE-ID
Posts: 26
|
|
Yes and Yes, I have a number of dies 223AI, 7TCU, 222, 223, 17 Rem and have tried them all. Last night I dug through a box I got at an auction and found a forming die from 223 to 17 Rem, bingo it worked, it took the base down another .002 to .0025 smaller than all the other dies. They will run thru my AR just fine now at .373. The small base die was just a click away and some how I resisted. The brass I am resizing is bulk mil stuff I have had a number of years it measures about .375 to .376 and factory nonfired stuff is measuring .372 to .373.
Get that Can yet? What one is it? I have had most everything with a large enought barrel threaded that is 30 cal or less. Just got back my 10-22 and what a hoot...
Last edited by sten668; 02-07-2010 at 06:25 PM.
|

02-21-2010, 01:42 AM
|
Senior Member
|
|
Join Date: Jan 2010
Posts: 118
|
|
300/221 brass
Thanks for the suggestions! I have a Harbor Freight fairly close to my home and after reading thru the article had to give this method a try.
Unfortunately, the first saw only turned on about a half dozen times, then the switch went out. The second one is still working. The very first thing that should be done after unpacking it is to remove the blade cover and reinstall the screw that holds the blade in place with Loc-tite or similar compound! The blade on my assembly almost came completely undone while cutting brass.
I used the suggested method with an old .308 case but was having a hard time getting even cuts so I tried this...
Take a 1 1/2" x 1/2" piece of wood and cut two lengths between 4" and 6":
Place them together and drill a 1/4" pilot hole:
Using the pilot hole drill out to 3/8":
Now that your working with a 3/8" hole, use a 3/8" spade bit and drill to the depth of the original .223 shoulder:
Set the new wood channel in-line with the .308 case, once aligned tighten the clamp:
With this setup I was able to get a good, clean, straight cut on the brass and minimize the work needed on the much more exact trimmer blades:
|

02-21-2010, 04:20 PM
|
Junior Member
|
|
Join Date: Feb 2010
Posts: 23
|
|
Scale
As for the brass I use to make .300 Whisper, yes, I will sort it by head stamp. I will most likely sort my LC stuff by year as well, just to provide another level of uniformity.
As for the .223 I process, I won't sort by head stamp.
jonblack
|
Thread Tools |
|
Display Modes |
Hybrid Mode
|
Posting Rules
|
You may not post new threads
You may not post replies
You may not post attachments
You may not edit your posts
HTML code is Off
|
|
|
All times are GMT -4. The time now is 12:48 AM.
|