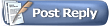 |
|

07-26-2005, 06:47 AM
|
Junior Member
|
|
Join Date: Jul 2005
Posts: 2
|
|
Learning to weld.
Hi! Okay, this is my first post in quarterbore. And this is the first post in this category of welding. It is the right time. I just bought a Harborfreight spot welder. It is amazing to make steel melt together. A long time ago, I was taught how to braze with an oxyacetylene torch and did auto body work with it.
Where have you gone to learn how to weld? TIG seems to be my aim. I plan to take a course at the local community college. What courses should I start with?
Thanks,
OrdnanceGuy
|

07-26-2005, 12:50 PM
|
 |
Administrator
|
|
Join Date: Dec 2004
Location: Valley Forge, PA
Posts: 1,598
|
|
I had a similar thread looking for advise before as I am kind in the same boat... In my youth I managed to play with a stick welder a little and managed to do some crude welding but nothing complicated... I have a very old Sears Arc welder that I bought at a yard sale for a whopping $10 and it works a little but I plan to buy a Mig/Arc setup to start my learning curve....
But... I am also listening to any suggestions on where to start!
|

07-27-2005, 09:36 PM
|
Senior Member
|
|
Join Date: Feb 2005
Posts: 111
|
|
My best friend wemt to a local High School Tech Center to learn welding. Now, he does it as a profession (5+ years later).
I have considered it, but for me, it would only be a hobby.
If you know someone who is a WELDER, get them to teach you. My buddy has gotten me a good ways. Almost look decent. But, by no means professional though.
KillJoy
|

07-28-2005, 11:37 PM
|
Junior Member
|
|
Join Date: Jul 2005
Posts: 2
|
|
Some Info for ya
I have been a “hobbyist welder” for over 15years, I’m not an expert on welding by any means but I can give you my “2-cents worth” as well as my experiences. As you know there are many different processes i.e. Stick, TIG, MIG, Gas, Plasma and Laser; those are the most popular. Each has its advantages and disadvantages; I’ll try to outline the basics of each later on.
One of the most important pieces of equipment regardless of which process you choose, is your safety gear. Buy a nice Miller auto darkening helmet, they are kind of expensive around $300-$400, it’s so much nicer to be able to see where your starting your weld, opposed to doing the “old head flip” this alone will improve your welds special on pieces that require precise welds. Proper gloves depending on the type of welding your doing, the two basic types fall into either insulated from heat i.e. these are your big thick gloves used for stick, mig and the more precise thin deer skinned gloves used in TIG etc… Along with other protective clothing, stick MIG Plasma all “shoot” off hot sparks as you weld so therefore you need to protect your body and surroundings from these sparks. Regardless of the process your also need to protect yourself from the UV rays not only to your eyes but your skin. So in a nutshell buy a good helmet!!
Here are a few details about the different process there’s a lot more to each but this should give you some idea as to what process you need to be looking for.
Stick Welding:
Advantages: The ability to weld in the wind (self shielding), forgiven to not having perfect joints and clean metal and relative easy to learn (cheap start-up cost) Fast welds
Disadvantage: not very precise on small intricate work and leaves slag that must be cleaned off. Heats up the surrounding metal more. Flying Sparks. Most cases you cant weld very thin metal. Stopping before competing a weld require you remove the slag and grind out the area.
Uses: Great for major construction of buildings and farm type work.
MIG Welding:
Advantages: More precise than stick. The ability to use self shielding wire or solid wire. Solid wire (where you use a separate shielding gas 75argon/25Co2 mix most cases) produces good results on most metals. Fairly easy to learn. Fast welds. Simi forgiven regarding metal/joint prep.
Disadvantages: Heats up the surrounding metal. Flying Sparks, depending on the shielding method you may or may not have to remove slag. Not easy to do weld very small parts with out warping. Stopping before competing a weld require you remove the slag and grind out the area. Depending on the shielding method you may(gas) or may not(flux-core) need a controlled environment.
Uses: Auto body work, farm type work, fast production work, furniture, BBQ’s etc… basic welding above stick.
GAS Welding: I never welded with gas so I can’t guide you on this process.
TIG Welding:
Advantages: Very precise and controlled welding. If you have a machine with AC you can weld aluminum and other non-ferrous metals. You can weld with out the use of a filler rod if the joints are overlapping etc.... i.e. join the two pieces together by simply melting them into each other. This of course takes away some the strength from the joint, so you need to know the how the part is to be used etc…and use filler rod if you need the joint to be as strong as the rest of the material or stronger. The ability to weld thin material, control heat to the weld area makes very strong welds etc… Not to mention very pretty welds. And no splatter, very clean it’s the “white collar job” of the welding world.
Disadvantages: Difficult to learn and master. Start-up cost, slow welding, controlled environment needed i.e. no wind, metal must be very clean, you will spend more time in prep work than welding time. 220volt needed unless you get a newer inverter type (big cost there for a ac/dc machine)
Plasma and laser: yes there is plasma welding not just plasma cutters, the cost of both plasma and laser welders are out of reach for most hobbyist, and are most of the time they are ran by CNC machines.
So to someone starting out in welding I would say take a class before you buy any equipment, this way you will get hands on with different machines and see what’s best for you and your application. I have had cheap $300.00 MIG’s and $2,000 MIG’s, stick welders “buzz boxes” along with TIG’s in the past, my current set-up is a TIG (see photo) Miller 180SD, Miller Coolmate 3 water cooler, size 20 tig torch and a Miller cutmate 375 plasma cutter, given the type of welding I do this is the best set-up for me, I can weld aluminum, titanium, stainless and carbon. Given my set-up I can weld about anything I need to. If you take a class I’m sure they will explain everything in great detail about the different process, I just wanted to give you a little info. If I can be of any further help just ask. Also you need to think about the type of metal you will be welding.
I would say this in closing if you cant take a class for whatever reason and don’t have the money to invest in equipment you best bet is to still buy that good Miller helmet, and buy one of the $300 flux-core MIG’s like they have at Home Depot/Lowes and a right angle grinder get some scrap metal and start learning. Now you have to look at this machine as a learning tool its not going to be welder that’s going to last forever or produce welds that would stand up to x-ray standards, and even thought you can set them up to run a shielding gas don’t waste your money, just use it as a flux-core machine and a learning tool. But that $300 investment you made on the helmet will carry over right into that new Miller TIG machine. You can also check with a local welding supply house and see what machines they have used, I bought my plasma cutter used for $1,100 which is about $400 cheaper than they were new it was a demo unit. I used it for about a year and then it stopped working but it still had the Miller 3year warranty on it so it was fixed for free.
Hope this helps, Now I need some help on 300Whisper Loads.
Texas-Whisper (Jimmy)
|

12-11-2005, 02:07 PM
|
Junior Member
|
|
Join Date: Dec 2005
Location: western PA
Posts: 1
|
|
OrdinanceGuy,
I learned to weld from my Dad, when I was a kid. He had a Lincoln stick welder and a oxy/acet outfit. I've been welding and cutting ever since. Probably by now, you have taken your welding course. If you want to learn more about welding, here is a link to a excellent info source http://www.khake.com/page89.html
|

12-13-2005, 11:36 PM
|
 |
Junior Member
|
|
Join Date: Dec 2005
Location: Edmonton, Alberta, Canada
Posts: 14
|
|
Yeah. . I've got my Canadian second year welding titcket. . if anyone has any questions
|

06-23-2006, 03:32 AM
|
Junior Member
|
|
Join Date: Jun 2006
Location: Mississippi
Posts: 2
|
|
I have been a pipewelder for 25 years now,my mom taught me at age 14.I take it you guys are only wanting to weld at home,on home projects.Contact your local welding supply shop.They will know of local courses in your area,also they know alot of your local welders who might give you a crash course.  Max has also given you some good info links.
If there are any questions or help I can give you guys email at Cayotekiller@yahoo.com or post it here
|

12-18-2006, 08:15 AM
|
 |
Junior Member
|
|
Join Date: Dec 2006
Location: Peoples Republic Of New Jersey
Posts: 11
|
|
Quote:
Originally Posted by Texas-Whisper
Stick Welding:
Advantages: The ability to weld in the wind (self shielding), forgiven to not having perfect joints and clean metal and relative easy to learn (cheap start-up cost) Fast welds
Disadvantage: not very precise on small intricate work and leaves slag that must be cleaned off. Heats up the surrounding metal more. Flying Sparks. Most cases you cant weld very thin metal. Stopping before competing a weld require you remove the slag and grind out the area.
Uses: Great for major construction of buildings and farm type work.
MIG Welding:
Advantages: More precise than stick. The ability to use self shielding wire or solid wire. Solid wire (where you use a separate shielding gas 75argon/25Co2 mix most cases) produces good results on most metals. Fairly easy to learn. Fast welds. Simi forgiven regarding metal/joint prep.
Disadvantages: Heats up the surrounding metal. Flying Sparks, depending on the shielding method you may or may not have to remove slag. Not easy to do weld very small parts with out warping. Stopping before competing a weld require you remove the slag and grind out the area. Depending on the shielding method you may(gas) or may not(flux-core) need a controlled environment.
Uses: Auto body work, farm type work, fast production work, furniture, BBQ’s etc… basic welding above stick.
.
Texas-Whisper (Jimmy)
|
Jimmy is Correct.
You can weld aluminum with a standard MIG welder, but you need to change your Gas to Pure Argon, Wire roll needs to be changed to aluminum wire, strongly suggest the replacement of the feed tube. Warning if your MIG welder is not 200 amps you most likely are wasting your time. Further blow out and clean clean your MIG welder inside. Aluminum takes allot of current to weld. If you want to try you should use the "Push" method in other words instead of dragging the welding tip push in to the weld. Second problem any time with aluminum is "Over heating" unlike steel aluminum will just vaporize.
Last note: People I know who weld Aluminum with MIG, generally leave one Machine ONLY ALUMINUM.
Stick Welding, in a conversation with Quarterbore, he told me of a person who welder the rails into an AK sheet metal receiver. While I am sure this could be done this I would classify this as an "Expert" task only and would not recommend this to the amateur.
Stick welding is great for very heavy projects such as a trailer hitch but is not known for it fine use.
Last note, from time to time I hear of the sales of “Special” rods for Aluminum, one other special metal, for stick and torches. Beware. Some times they work most of the time not. The bond is more like solder, and no strength is really added.
Face/ eye protecting……This speaks for it’s self. A run to the ER at 11:00 PM and your eyes feel like sand was tossed in them, is unpleasant at best. An Ark viewed unprotected for less than one second, can cause this.
I find welding fun, you should as well. I recommend start with the old “stick welder” bought at the tag sale, lots of scrap. If you have the time adult education courses at the local community collages is the best but time does not always allow this.
Have Fun and Good luck
David
|

07-12-2007, 10:31 AM
|
Junior Member
|
|
Join Date: Jul 2007
Posts: 2
|
|
Quote:
Originally Posted by Davidfxs
Jimmy is Correct.
You can weld aluminum with a standard MIG welder, but you need to change your Gas to Pure Argon.
David
|
You also need the aluminum kit for the lead. I have a small Lincoln 175 that I use for steel and aluminum. I repair small displays and have to change the spool every so often. To make this a little easier, I just run straight argon for both metals. The salesperson at my welding supply described it perfectly: "Trying to weld aluminum with a 6' lead is like trying to push a chain from the last link"
Someday I'll shell out the cash for either a TIG or spoolgun/mig combo.
|

07-12-2007, 09:24 PM
|
 |
Member
|
|
Join Date: Dec 2006
Posts: 86
|
|
Anyone else use the Lincoln Pro-Mig 140?
I just picked one up and haven't use it yet. Looking for opinions on this rig
|
Thread Tools |
|
Display Modes |
Linear Mode
|
Posting Rules
|
You may not post new threads
You may not post replies
You may not post attachments
You may not edit your posts
HTML code is Off
|
|
|
All times are GMT -4. The time now is 12:59 AM.
|